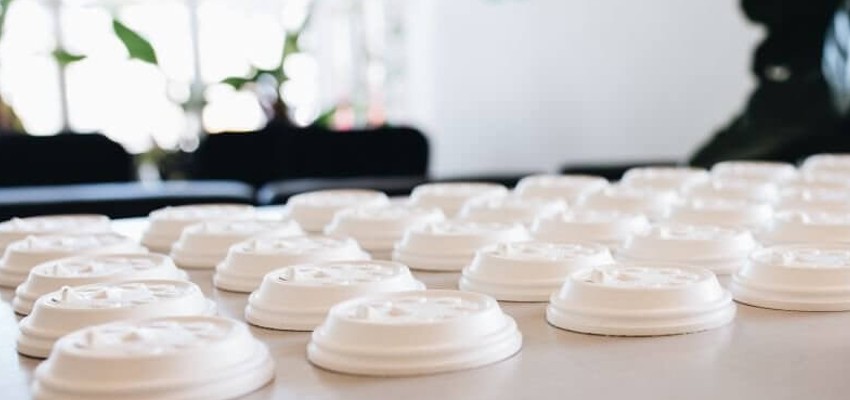
PulPac Expands Global IP for Dry Molded Fiber
The patented DMF technology consumes lesser energy and water as compared to traditional fiber-forming methods, in addition to significantly lowering carbon dioxide while enabling high-speed production of fiber-based packaging.
PulPac has announced further patent grants for its pioneering cellulose forming technology that makes it possible to replace single-use plastics with competitive fiber-based alternatives in sustainable packaging.
The company’s most general patent, which already has been granted in big parts of the world, is now also granted in Colombia. Furthermore, a new patent comprising hole punching of Dry Molded Fiber products has been granted in Sweden.
The granted patent in Colombia fortifies PulPac’s global ownership of the core technology of Dry Molded Fiber (DMF). The patent relates to a method, apparatus, and product where air-formed cellulose is pressed in a forming mould within given temperature and pressure intervals and has already been granted on important markets such as China, Europe, USA, Japan, and Russia.
List of Pulp and Paper Companies: Paper Companies in Maharashtra
Compared to traditional fiber forming methods the DMF technology consumes less energy and water in addition to significantly lowering CO2 while enabling high-speed production of fiber-based packaging. It can be used for forming cellulose products in a wide variety of shapes, at costs that are competitive with plastics.
Speaking about the patent portfolio, Mr. Peter Ekwall, IP Manager at PulPac, comments, “The world needs to move away from plastics, and we will continue to spearhead innovation and grow the DMF patent portfolio to support the urgent transition to fiber-based packaging. With strong and global IP, we advance our licensee’s position and the incentive to drive change for a better future.”
PulPac has also been granted a patent in Sweden relating to a system and a method for dry forming a three-dimensional cellulose product using PulPac’s unique DMF technology. The patent is especially directed towards a moulding feature allowing for punching one or more holes in the product already in the forming mould. This is advantageous when manufacturing lids for hot or cold drinks but can also be used in other applications.