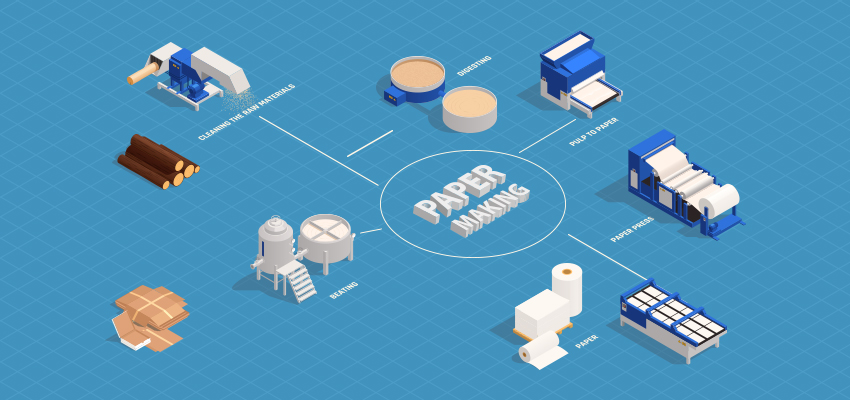
Understanding the Pulping and Papermaking Process
Paper can be defined as a thin sheet essentially made from cellulose pulp derived from wood and a number of different lignocellulosic materials like – cotton, rice, grasses, bagasse or wheat straw (agricultural residues) for producing different kind of paper for different uses. In fact, paper finds its use in a variety of applications in – writing & printing, packaging, decorating, cleaning, filter paper, wallpaper, books, laminated worktops, toilet tissue, currency and security paper and a number of other areas.
The history of papermaking can be traced back to China, at least as early as 105 CE. The story of origin of the versatile material states that it came into being as an alternative writing material to silk. The papermaking process was introduced in Europe in the 12th century. Earlier, the most common fiber source for paper production before the industrialization of the process took over was recycled fiber extracted from used textiles called rags, derived from hemp, linen and cotton.
Today, the pulp and paper mills deploy complex procedures in the production combining a gamut of different processes including – wood preparation, pulping, chemical recovery, bleaching, and papermaking. Processing options and the type of fiber processed, amongst other things, are contingent on the final product to be manufactured at the mill.
Pulping – Producing pulp for papermaking
In the papermaking process, the production of pulp is the first and foremost step. The pulp may be produced from a variety of processes, namely, chemical pulping, mechanical pulping, and deinking. That is, while the pulp produced from virgin fiber can be produced by using chemical or mechanical means, pulp may also be produced by the repulping of paper which involves the deinking process of wastepaper. Thus, paper making is fundamentally a two-step process consisting of the conversion of a fibrous raw material to pulp, and then the pulp is converted into paper.
Also Read: The Process of Papermaking
In the chemical pulping process, lignin is separated from cellulose fiber to make pulp from wood. Cooking liquor is used to dissolve the lignin, which is then washed from the cellulose. Paper made from chemical pulp is also known as wood-free paper.
In the mechanical pulping process, there are two major mechanical pulps that we have to take into account – thermomechanical pulp (TMP) and groundwood pulp (GW). For the TMP process, wood is chipped and then processed in steam-heated refiners, where the chips are converted to fibers. For the groundwood process, debarked logs are fed into grinders to be made into fibers. Although the mechanical pulping process doesn’t remove the lignin which leads to a high yield, but the presence of lignin results in the paper produced to turn yellow and become brittle over time.
Finally, in the deinking process which entails paper recycling, either chemically or mechanically produced pulp can be used. Most recycled paper contains a proportion of virgin fiber; however, the recycled papers can be made from 100 percent recycled materials or blended with virgin pulp.
Papermaking Process
After the pulp making process is done, the pulp is then bleached and further processed, depending on the type and grade of paper to be made. So, the pulp is processed in a paper machine, where a paper web-like structure is made and the water is removed from it by the means of – pressing and drying.
Find list of Suppliers to Paper Mills: Paper & Paper Board Making Machinery
In pressing, the water is removed from the sheet by applying force. After the water is extracted out from the sheet, a certain kind of felt is used to collect the water. The process of drying entails the use of air or heat to remove water from the sheets. Earlier, the drying process was executed by keeping the sheets hanged like laundry. In the modern day and age, different kinds of heated drying mechanisms are utilised, the most commonly used being the use of steam-heated can dryer.
After these processes, paper then undergoes sizing wherein its physical properties are altered for use in various applications. The size press machine applies starch to paper in the middle of the dryer process so as to provide water resistance and surface strength to paper.
Then, in calendering process, calender comprising several steel rolls are made to rub the surface of the paper so as to smoothen and gloss the paper sheet. At last, paper sent out of the calender is wound on a reel and shipped as a product after finishing.